Conservation Strategies to Manage Your Air Compressor Energy Usage
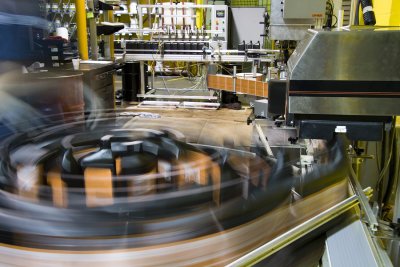
Whether you have a compressed air system that powers machine tools, material handling equipment, spray painting guns or any other type of commercial or industrial equipment, there are a number of ways you can increase your air compressor’s energy efficiency to reduce operating costs and even extend the life of your compressed air system. Because compressed air is one of the most expensive energy resources in a manufacturing or processing plant, any efforts taken to manage your air compressor energy usage will return significant savings each month. Here are some conservation strategies to help you get started.
Keep Your System Maintained
One of the best ways to keep your air compressor system running efficiently is to follow a routine maintenance schedule as recommended by the manufacturer or your air compressor service company in San Jose. On a similar note, be sure to have your air compressor serviced anytime you notice a change in performance or operation to keep things running efficiently.
Check for Leaks
Regardless of the size of your air compressor system, routinely check for leaks to minimize waste. Even a small leak can cost hundreds or thousands of dollars in additional energy costs each year. For example, a compressed air distribution system under 100 psi of pressure running 40 hours a week with a quarter-inch diameter leak can cost an additional $2,800 per year to run.
Look for Artificial Demands
“Artificial demand” in an air compressor system refers to the supply of higher air pressure than is required for the end-use application. In other words, if an application requires 50 psi but is supplied 100 psi, excess compressed air is used and wasted. To minimize artificial demands in your compressed air system, install pressure regulators at each end use and have your system and applications calibrated by an air compressor service technician in San Jose.